2023年12月4日
https://xtech.nikkei.com/atcl/nxt/column/18/02665/112800001/
日経クロステック/日経Automotive
2023.12.04
有料会員限定
全3116文字
- https://6f405bd53f1e976b3167f6cabfcf1879.safeframe.googlesyndication.com/safeframe/1-0-40/html/container.html
- https://6f405bd53f1e976b3167f6cabfcf1879.safeframe.googlesyndication.com/safeframe/1-0-40/html/container.html
- https://6f405bd53f1e976b3167f6cabfcf1879.safeframe.googlesyndication.com/safeframe/1-0-40/html/container.html
電気自動車(EV)市場の現状や各自動車メーカーの技術的な特徴を把握するため、本コラム「世界EV総覧」では日本・米国・欧州・中国・韓国などの主要メーカーが販売するEVを整理する。散らばっている情報をまとめ、比較することで各社のEV戦略や車両の優劣が見えてくる。今回は、トヨタ自動車の全体動向をお伝えする。
トヨタはパワートレーンの電動化において「マルチパスウェイ」戦略を掲げる。主力のハイブリッド車(HEV)を筆頭に、EVやプラグインハイブリッド車(PHEV)、燃料電池車(FCV)、水素エンジン車など幅広い開発を進めている(図1)。
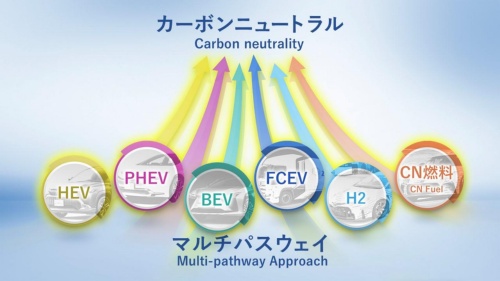
図1 電動パワートレーンは全方位で
「マルチパスウェイ」戦略を掲げ、2050年のカーボンニュートラル(温暖化ガス排出量の実質ゼロ)を目指す。(出所:トヨタ)
[画像のクリックで拡大表示]
EVにおいては、2022年5月に発売した「bZ4X」でトヨタ初となるEV専用プラットフォーム(PF)を導入した。トヨタが2022年に販売したEVは約2万4000台にとどまる。低空飛行を続けるbZ4Xの教訓を生かし、次世代EV専用PFの開発を進めている。2026年に実用化する目標である(図2)。
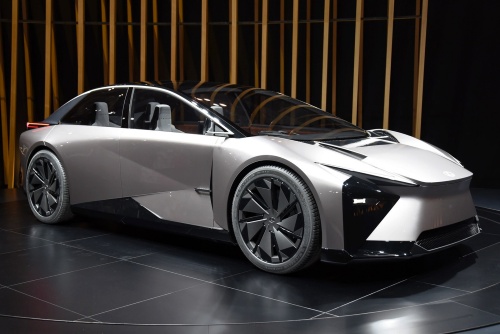
図2 「レクサス」ブランドのEVコンセプト「LF-ZC」
このモデルをベースに開発したモデルを2026年に発売する予定。次世代の車載電池を採用し、1000kmの航続距離(CLTCモード:中国の独自の走行サイクル)を目指す。(写真:日経クロステック)
[画像のクリックで拡大表示]
トヨタは2026年までにEVの新モデルを10車種投入し、年間販売台数を150万台まで増やす計画である。2030年までにトヨタと「レクサス」ブランドで30車種のEVモデルをグローバルに展開し、年間350万台まで生産できるようにするという。
中国ではBYDと共同開発したEVも
トヨタが現在、グローバル展開しているEVはbZ4Xと「レクサスRZ」の2モデルである(図3)。いずれもSUV(多目的スポーツ車)タイプで、日本の他、欧州や米国、中国などで販売している。
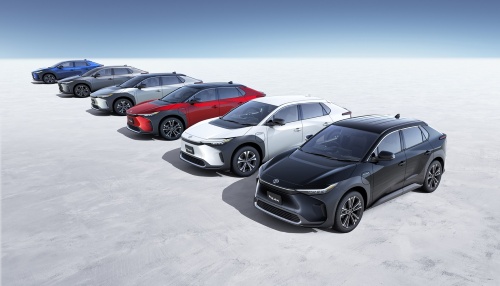
図3 トヨタの量産EV「bZ4X」
2022年に発売した。(写真:トヨタ自動車)
[画像のクリックで拡大表示]
グローバルモデル以外に、トヨタは中国専用モデルも用意する。1つがEVセダン「bZ3」で、トヨタと中国・比亜迪(BYD)が合弁で設立したBYD TOYOTA EV TECHNOLOGYカンパニー有限会社(BTET)と一汽トヨタが共同開発した。bZ3の開発リーダーを務めたのが、トヨタからBTETに出向して最高技術責任者(CTO)を務めていた加藤武郎氏である。同氏はトヨタに復帰し、同社が2023年5月に立ち上げたEV事業の専任組織「BEVファクトリー」のトップ(President)に就任した。
中国では、広州汽車との合弁である広汽トヨタブランドからセダン「iA5」も発売中である。広州汽車傘下の電動車メーカーである広汽新能源の「Aion S」や、広州汽車とホンダの合弁である広汽ホンダの「EA6」の兄弟車だ。
開発および部品調達に関しては、グローバルモデルであるbZ4XやレクサスRZは、デンソーやアイシンをはじめとするトヨタグループでの連携が強い。中国専用車は部品も現地調達が中心で、例えばbZ3の電池はBYD製である。
生産拠点は、国内に2カ所ある。bZ4XとレクサスRZは元町工場(愛知県豊田市)で生産している。小型SUVタイプのEV「レクサスUX300e」はトヨタ自動車九州の宮田工場(福岡県宮若市)が担当する。
トヨタは海外でのEV生産も準備中である。2025年から米国ケンタッキー州にある生産拠点Toyota Motor Manufacturing Kentucky(TMMK)で、EVの新型車となる3列シートのSUVを生産することを決めた。米国では、グループの豊田通商と共同で、ノースカロライナ州に車載用電池工場を建設し2025年に稼働させることも予定する。トヨタは欧州でもEVを現地生産することを検討している(図4)。
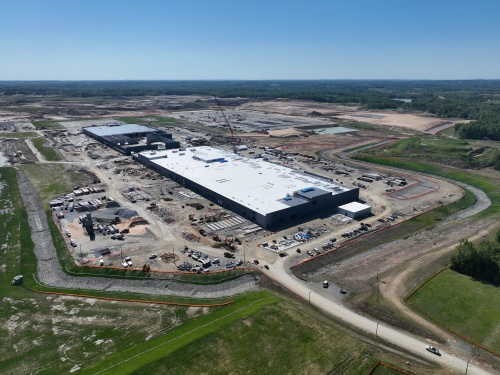
図4 将来の電動車需要の伸びに対応できるよう電池工場を建設
新型EVに搭載する電池を生産するToyota Battery Manufacturing, North Carolina(TBMNC)に21億ドルを追加投資する。(写真:トヨタ自動車)
[画像のクリックで拡大表示]
「bZ4X」はリースから一般販売へ
先述した通り、トヨタがEV専用PFを適用したモデルを展開し始めたのはbZ4Xから。それ以前は、エンジン車とPFを共用しつつ、EVに仕立てていた。一例が、同社が2020年に中国専用車として発売した「C-HR」のEVモデルと兄弟モデル「IZOA」である(図5)。トヨタの車両開発手法「TNGA(Toyota New Global Architecture)」に基づいて開発した小型FF(前部エンジン・前輪駆動)車向けの「GA-C」を適用した。レクサスブランドから発売したUX300eも、C-HRやIZOAとPFや電動パワートレーンを共用する。
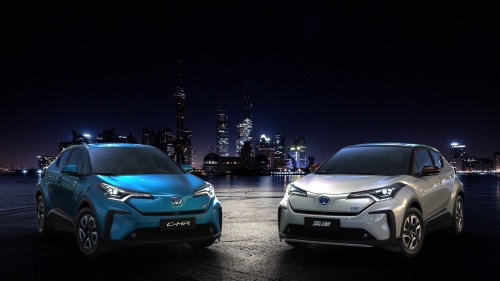
図5 中国専用EVの「C-HR」と「IZOA」
トヨタブランドとして中国初投入となるEVで、2020年に販売を開始した。(写真:トヨタ自動車)
[画像のクリックで拡大表示]
bZ4Xを皮切りに実用化したEV専用PF「e-TNGA」は、SUBARU(スバル)と共同開発したもの。モーターやトランスアクスル、インバーターを一体化して小型化を図った電動アクスル(e-Axle)や、充電機能と電力分配機能を集約して小型化したElectricity Supply Unit(ESU)をトヨタとして初採用。これらの大物部品を低い位置に搭載したことも重心を低くするのに寄与した。
トヨタは、bZ4Xをサブスクリプション(定額課金)専用モデルとして展開を始めた。グループ会社のKINTO(キント、名古屋市)を通じた提供で、月額料金は4年目までは国の補助金も含めて8万7120円である。サブスクに限定して大きな理由は、「電池の劣化状態を把握し続けるため」(トヨタのEV技術者)だった。初のEV専用PF適用モデルだけに、慎重な姿勢がうかがえる。トヨタはbZ4Xを部分改良し、2023年11月に発売。これまでのリース販売に加えて、店舗での一般販売を開始した。
欧州では、MPV(多目的車)タイプのEV「Proace City Verso Electric」を2021年に発売した。欧州Stellantis(ステランティス)の旧グループPSAからOEM(相手先ブランドによる生産)調達したモデルである。
ギガキャストや全固体電池を準備中
トヨタは2026年に投入する次世代EVに向けた開発を急ぐ。投入する目玉技術が新工法「ギガキャスト」である(図6)。ギガキャストは、数十点の板金部品で造る部品を、アルミダイカストの一体物として成形する生産技術である。車体後部側のアンダーボディーに適用すれば、86個の板金部品を33工程かけて生産していた部分を1部品・1工程に集約できる。同社は2018年ごろに大型のダイカストマシンを購入。試作検討を進める脇をすり抜けて、レガシーを持たない米Tesla(テスラ)がギガキャスト(テスラは「メガキャスティング」と呼ぶ)の実用化で先行した。
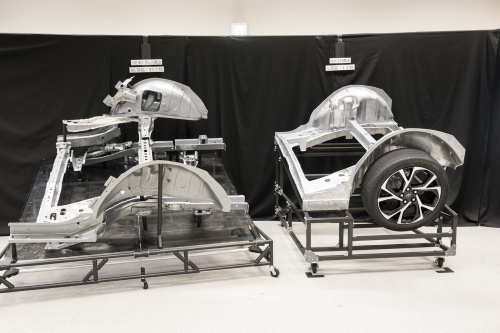
図6 ギガキャストで成形したリアアンダーボディー(右)
一体成形のため、部品点数を1点にできる。これに対し、現行のリアアンダーボディー(左)は鋼板をプレス成形した小物部品を溶接でつなぎ合わせて造っている。そのため、部品点数は86点で、工程数は33もある。(写真:トヨタ自動車)
[画像のクリックで拡大表示]
「これまでの“しがらみ”を断って新しいことにチャレンジする」。トヨタ副社長の中嶋裕樹氏は、2023年4月に開いた「新体制方針説明会」で変革の重要性を訴えた。しがらみの内容には言及しなかったが、ギガキャスト構想も念頭にあったのだろう。これまで同社はボディー部品の多くを外部調達してきたが、ギガキャストでは内製比率が高まる見込み。鋼板からAl材への移行で材料メーカーにも影響が出る。それでも、工程や工場投資を1/2にする上でレガシーは足かせになり得る。
2027~28年を目標に、全固体電池の実用化も目指す(図7)。2026年に同社が導入する次世代EVへ搭載する液系の次世代電池に対して、満充電時の航続距離(以下、航続距離)を20%伸ばせるものだ(空力や軽量化などの車両効率向上分を含む。航続距離に関し、以下同じ)。同次世代EVに搭載すれば、航続距離は1200kmほどになるとみられる。

図7 全固体電池の試作品
EVへの全固体電池搭載に挑むことを決めたのは、「電池の耐久性を克服する技術的なブレークスルーを発見したため」(トヨタ)とする。(写真:トヨタ自動車)
[画像のクリックで拡大表示]
全固体電池の肝となる固体電解質に関しては、出光興産との協業を決めた。両社から数十人を募ってタスクフォースとし、年間最大数百トン規模の硫化物系固体電解質を生産するパイロットプラントを出光興産の千葉事業所内に設けて、2027~28年を目標に量産技術を実証。同時に材料の安定調達のスキームを構築する。この2027~28年には台数は限定的ながら全固体電池搭載のEVを発売する見込みだ。